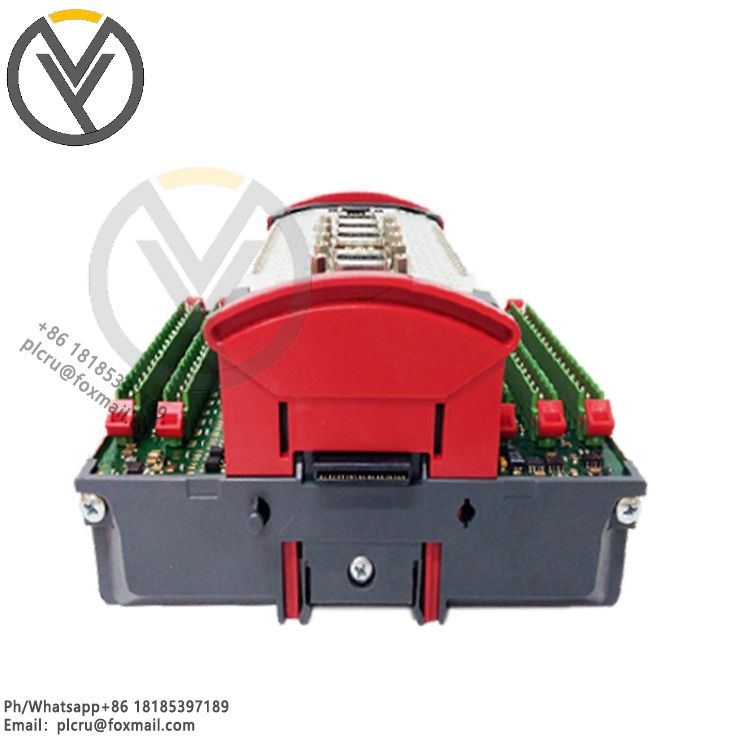
MOOG G35HOCA4NSM5HO Servo Valve
Delivery time 3 days
Product origin New/used
Email plcru@foxmail.com
Mobile/wechat /WhatsApp +86 18185397189
MOOG G35HOCA4NSM5HO servo valve is a high-precision control component produced b
MOOG G35HOCA4NSM5HO servo valve is a high-precision control component produced by MOOG, which is widely used in automobile, machinery, textile and other industries. The following is a detailed introduction to the servo valve:
1. Basic features
High precision: MOOG servo valve adopts advanced hydraulic transmission technology, with the advantages of fast response speed, high precision, stability and reliability.
Wide applicability: This servo valve is widely used in various industrial control systems, especially in occasions requiring high-precision control and adjustment.
2. Technical parameters
Working pressure range: The working pressure of valve ports P, A and B does not exceed 350bar (5000 psi); the working pressure of valve port T refers to the specific data of each series of valves.
Temperature range: Ambient temperature is between -20℃ and +60℃ (-4℉ to +140℉); oil temperature is between -20℃ and +80℃ (-4℉ to +170℉).
Sealing ring material: Nitrile rubber, fluororubber, etc. Other sealing materials can be provided according to user needs.
Working medium: petroleum-based hydraulic oil (DIN51524).
Viscosity: value 15-100mm²/s; allowable value 5-400mm²/s.
Installation direction: can be installed in any position, supports fixed or movable installation.
3. Working principle
MOOG servo valve is an electro-hydraulic conversion element and power amplifier element, which converts electrical signals into high-power hydraulic energy (flow and pressure) output. The servo valve is composed of a DC proportional solenoid, a valve core, a valve sleeve, a valve body, a displacement sensor and a control amplifier. When the input coil is fed with current, the displacement sensor linearly converts the armature displacement of the electromagnet into a voltage signal output, and the control amplifier compares and amplifies the command signal and the displacement response signal, and finally outputs a current signal to drive the valve core to move, thereby achieving precise control of the flow rate.